|
|
|
|
|
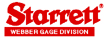 |
|
|
|
Back to the HOME PAGE
|
|
CALIBRATION / RECALIBRATION & REPAIR SERVICES
|
|
|
|
Display NVLAP Lab Code 200038-0 Accreditation
|
|
|
|
|
 |
|
|
Download NVLAP Lab Code 200038-0 Certificate and Scope of Accreditation
|
|
All our reference standards are calibrated directly by NIST. Statistical methods are used to control and monitor all our
reference and transfer standards. Our detailed documented histories allow us to give the lowest uncertainties possible.
Reported measurement uncertainties are based on a 95% confidence level (two standard deviations). Factors included
in the stated uncertainty are derived from a detailed error analysis, and are based upon experimentation whenever
possible or industry consensus from estimates derived from NIST publications. Experimental checks of the stated
uncertainties are made using laboratory comparisons involving both internal repeatability studies and external comparisons
with other calibration laboratories.
|
|
|
|
|
|
|
LINEAR GAGE BLOCKS
|
|
|
|
|
Commercial Calibration procedures are performed by direct comparison to master gage blocks of similar size.
Information about the calibration is recorded by our computer systems that includes the materials of the gage blocks,
pressure and tip radius of the comparator, the temperature of the gage blocks, and the environmental conditions during
the calibration. Individual applied correction factors are recorded as well as the results of any calculations. The
uncertainty is computed for each measurement based upon the current conditions during the calibration. The validity of
the calibration is tested by comparing the standard deviation of three measurements against an expected standard
deviation derived from historical data. Compare our commercial calibration pricing here.
Master Calibration procedures are also performed by direct comparison to master gage blocks, but a second master,
sometimes refereed to as a control block is also used in the process. The purpose of the second master is to generate
known difference readings from the first master which are used to control the measuring process using SPC techniques.
The validity of the calibration is tested by comparing the standard deviation of three measurements against an expected
standard deviation derived from historical data as well as comparing the expected average and standard deviation of the
measurements of the control blocks.
Laboratory Calibration procedures are performed to achieve the lowest possible uncertainty of measurement, but
only those blocks with the best geometry (parallelism and flatness) and of Webber croblox® material may be tested.
Laboratory Calibrations are restricted to Webber rectangular style croblox® gage blocks of Webber grades LM or AA,
GGG Grades 0.5 and 1, and B89 Grades 00 and K. When a test block is compared to one of our master blocks of the
same croblox® material, the correction factors for temperature and deformation are significantly smaller. This greatly
reduces the uncertainty of measurement.
Laboratory Calibration procedures are performed as three separate sets of Master Calibrations using different operators,
master gage blocks sets, and control blocks. Each set of measurements must pass all the statistical tests required of a
Master Calibration. The three sets of readings are averaged together to give the reported result.
The table below gives a comparison of our uncertainties for the calibration procedures described
above.
|
|
. Uncertainties (in microinches, k=2) Uncertainties (in microinches, k=2)
For gage blocks 4-inches and below in length For gage blocks 5-inches and above in length
|
|
|
|
|
|
|
General Uncertainty
Formula
|
|
3.0 µin.
|
2.4 µin.
|
U = 2.0 + 1.0L |
|
2.0 µin.
|
1.8 µin.
|
U = 1.2 + 0.7L |
|
1.5 µin.
|
1.4 µin.
|
U = 0.7 + 0.7L |
|
|
Typical for
10-inch block
|
General Uncertainty
Formula
|
|
10.0 µin.
|
U = 5.0 + 0.35L |
|
7.0 µin.
|
U = 3.5 + 0.25L |
|
n/a
|
n/a
|
|
|
.
Uncertainties (in micrometers, k=2) Uncertainties (in micrometers, k=2)
For gage blocks 100mm and below in length For gage blocks 125mm and above in length
|
|
|
|
|
|
|
General Uncertainty
Formula
|
|
0.08 µm
|
0.06 µm
|
U = .05 + .001L |
|
0.05 µm
|
0.045 µm
|
U = .03 + .0007L |
|
0.04 µm
|
0.035 µm
|
U = .018 + .0007L |
|
|
|
General Uncertainty
Formula
|
|
0.25 µm
|
U = .13 + .00035L |
|
0.18 µm
|
U = .09 + .00025L |
|
n/a
|
n/a
|
|
|
|
The actual uncertainty of measurement may vary due to the condition of the gage block being measured.
|
|
|
|
Explanation of the Linear Gage Block Calibration Certificate |
|
|
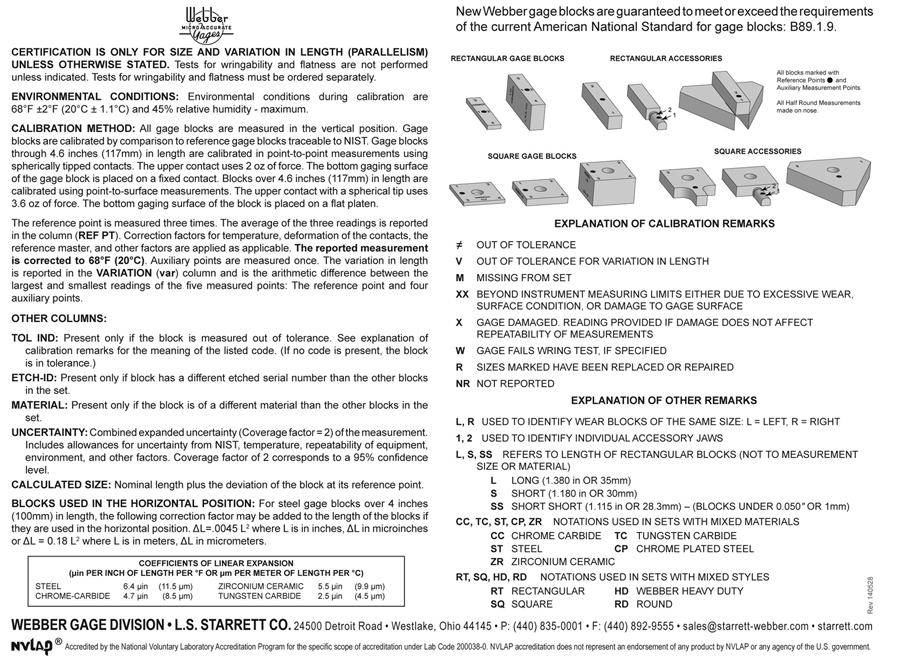 |
|
|
|
|
|
|
|
|
|
ANGLE GAGE BLOCKS and TRUE SQUARES
|
|
|
|
Calibrations are performed by direct comparison to master angle gage blocks of similar size using a pair of autocollimators
and a fine rotary table. First, the autocollimators are set using the master angle block. A "null" autocollimator reads the base
of the angle block and the "read" autocollimator reads the hypotenuse or the angle of the angle block. The angle block to be
calibrated is substituted for the master angle on the rotary table. The rotary table is adjusted until the "null" autocollimator
again reads zero. The difference of the "read" autocollimator plus the calibrated deviation of the master angle is the error of
the test angle block.
|
|
Grade of Angle Block
|
Dimensions of Angle Block
|
|
Reference or Lab Master
|
|
|
Calibration or Inspection
|
|
|
Working or Tool Room
|
|
|
|
|
|
|
|
|
The actual uncertainty of measurement may vary due to the condition of the angle gage block being measured.
The flatness of the base and hypotenuse has a large effect on the uncertainty of measurement.
|
|
|
|
|
OPTICAL POLYGONS
|
|
|
|
Calibrations are performed by direct comparison to a master indexing table using an autocollimator.
|
|
|
|
|
|
|
|
|
|
|
|
OPTICAL CUBES
|
|
|
|
Calibrations are performed by using the closure method. Using autocollimators, each 90° angle of the cube is compared to
the other three 90° angles on the axis of rotation which by definition must equal exactly 360 degrees.
|
|
|
|
|
|
|
|
|
|
|
|
OPTICAL FLATS
|
|
|
|
Calibrations are performed by direct comparison to a master optical flat. The flat to be calibrated is placed on a master flat
and viewed with a monochromatic light source. The interference pattern that is generated is interpreted by the operator to
fractions of a bandwidth and converted to microinches or micrometers.
|
|
Flatness: Best Uncertainty
|
General Uncertainty Formula
|
|
U(µin.) = 3.0 + 0.15 of Reading
U(µm) = .075 + 0.15 of Reading
|
|
|
|
|
|
|
|
|
|
|
REFERENCE BARS AND WEBBER DIGI-CHEK II® HEIGHT GAGES
|
|
|
|
Calibrations are performed in the vertical position by direct comparison to a master gage stack using a precision indicator.
The stack to be calibrated is placed along side the master gage stack on a transfer table in a controlled calibration chamber.
The transfer table allows the stacks to be moved to a fixed indicator rather than moving the indicator to the stacks on a
surface plate.
The transfer table is two parallel plates separated by closely matched ball bearings. This allows for nearly parallel movement
of the top plate. The surfaces of the transfer tables are calibrated using optical flats and held to less than a fringe band. This
can be compared to the tolerance of the best surface plates which typically have flatness tolerances of 100 microinches
(2.5 µm). By using a transfer table, the error of movement of the stacks is reduced to only a few microinches or a fraction of
a micrometer.
NOTE: WHEN PREPARING AN UNCERTAINTY BUDGET WHEN USING THESE GAGES, PLEASE CONSIDER THE
UNCERTAINTY FROM:
1) OUR CALIBRATION OF THE GAGE,
2) TEMPERATURE (COEFFICIENTS OF EXPANSION OF MATERIALS AND TEMPERATURE GRADIENTS)
3) THE SURFACE PLATE BEING USED IN YOUR MEASUREMENTS.
|
|
Typical Uncertainty
at 25 inches (625mm)
|
General Uncertainty Formula
|
|
U(µin.) = 10 + 2.5L
U(µm) = .25 + .0025L
|
|
|
|
|
|
|
|
MODEL 258 DIGI-CHEK Micrometer HEIGHT GAGES
|
|
|
Calibrations are performed in the vertical position by direct comparison to a master gage stack using a precision indicator.
The stack to be calibrated is placed along side the master gage stack on a surface plate in a controlled calibration chamber.
|
|
|
|
|
|
|
|
|
|
Back to the HOME PAGE
|
|
©2024, Webber Gage Division, The L. S. Starrett Co, Westlake, Ohio, 44145
|
|
Updated 24 June 2024 |
|
|
|
|
|
|
calibration
|
|
|
|
|
|
|
|
|
|
|
|
|
|
|
|
|
|
|
|
|
|
|
|
|
|
|
|
|
|
|
|
|
|
|
|
|
|
|
|
|
|